咪唑啉缓蚀剂的合成
近年来,我国陆地油田有相当一部分已进入注水开采的中、后期,油井综合含水不断上升,产出水矿化度较高,同时伴有大量侵蚀性物质,受这些综合因素的影响,在油气井注水开发中,从油水井地下管柱到地面管道和储罐及各种工艺设备都会遭到腐蚀,造成巨大的经济损失,严重的还会造成灾难性事故和环境污染。 对于含二氧化碳及硫化氢的高矿化度偏酸性的污水,咪唑啉类缓蚀剂具有很好的缓蚀效果。咪唑啉是含有两个氮原子的五元杂环化合物,除了主体杂环外,还有与杂环上N成键的具有不同活性基团支链和烷基碳链长度不同的疏水支链。疏水烷基碳链可以在金属表面附近形成一层有效的疏水层。所形成的疏水层,即可以对电极表面起到一定外围屏蔽作用,也能阻碍具有腐蚀性能的反应物在腐蚀界面上的迁移。活性基团支链可以显著提高缓蚀剂分子的溶解性,通常还可同金属表面的孤对电子形成配位键而产生化学吸附作用,而达到提高缓蚀性能得的作用。 |
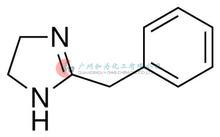 |
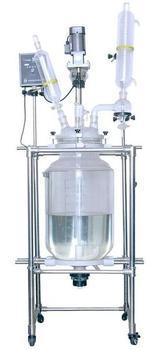 |
常用的合成咪唑啉的方法为:分别取一定量的脂肪酸、多胺和二甲苯放入装有温度计、回流冷凝管和分水器的三口烧瓶中,升温到140-150℃附近进行酰胺化反应,然后升温到180-250℃反应进行环化反应。反应结束后,即得到淡黄色的咪唑啉产物。根据具体使用环境,还可以用氯化苄、氯乙酸钠与咪唑啉发生反应,形成咪唑啉季铵盐。
咪唑啉与及其衍生物类缓蚀剂的合成主要受到生产的水及温度的影响:
(一)水的影响 在反应过程中酰胺化和环化两个过程都生成了水,但水的存在对反应的继续进行存在阻碍作用。原因主要是以下两点:第一,从化学动力学角度,酰胺化和环化反应所生成的水阻碍了正方向反应的进行,使整个合成反应减速;第二,在水存在的情况下,生成产物极其容易水解以及发生其他的副反应,使得产物的纯度降低。在这种清况下,对所合成咪唑啉中间体应尽快进行除水操作。通用的去除水方法有两种(1)真空法或氮气保护:进行第一次脱水,先对反应体系抽真空或通入氮气,使得反应物在非常低的压强下或氮气保护下充分地混合并进行加热处理,之后采用程序升温与逐渐降低压力或减少氮气的方法,除去体系中的水分,进行第二次脱水。(2)溶剂法:其中第一次脱水是在常压下进行的,是以甲苯或二甲苯做携水剂与水共沸,然后将水从容器中带出,以此推动反应的继续进行。再在减压的条件下进行升温,进行第二次脱水环化。其终点可以用反应生成的水和产物的酸度值来判断。这两种方法各有利弊:溶剂法的合成产物,反应温度很低,并且生成的产物不易变质变色,但反应终点的判断需要的时间较长,收率也比较低;而真空法存在的问题则是对整个反应过程所用仪器的密封性要求较高,否则生成物容易变质,原料中胺也较易被抽走,氮气法不仅氮气消耗量大,而且也容易将反应原料中的胺带走。也可以根据上述两种方法的特点,将其优缺点进行整合,前期溶剂法,后期真空或氮气保护法的混合法。目前,工业生产中大多数采用甲苯和真空脱水的方法。甲苯脱水法优点是出水比较平稳,多胺不易被抽出,但回收甲苯较为麻烦。真空脱水法的优点是,较简单,但多胺易被抽出,使生产物质中所含有的二酰胺过多。二酰胺为反应的副产物,一般情况下不能转化为咪唑啉类物质。并且不能进行季铵化反应,是合成咪唑啉产物中的主要杂质。生成物中二酰胺的百分含量被作为评定咪唑啉优劣的标志。二酰胺的含量过高,产物季铵化后极容易沉淀,最终产物的稳定性下降。 |
(二)反应温度的影响 反应温度是制备咪唑啉缓蚀剂反应中的重要因素。咪唑啉中间体的合成过程是经过两步脱水。国内对咪唑啉环化过程的反应温度段的温度高低进行了很深入地研究,但并没有达成一致认识。有研究认为在酰胺化脱水段,温度在140-160℃,反应时间在1-1.5h较为合适。在环化脱水阶段,温度应在180-250℃,最高的反应温度不应超过270℃,反应的时间应在1.5-2h较为理想。而也有研究指出环化脱水反应的温度,一般应在240-250℃,反应时间在8-16h不等。还有研究说明在含有携水剂的情况下,150℃也并不是最佳的反应温度,逐步升温的方法更合理和更有优势。 屈人伟等将环烷酸和二乙烯三胺按1:1.2的摩尔比混合,在100-120℃下预反应0.5小时,然后升温至180℃反应1小时,再升温至210℃反应1小时,得到咪唑啉。将合成的咪唑啉分别与环氧乙烷和氯化苄按摩尔比1:7和1:1在一定条件下反应,得到深褐色环烷酸咪唑啉的乙氧基化产物和季铵化产物,在200 mg/LH2S-3%NaCl-H2O污水体系中评价了制备产物的缓蚀性能。对于乙氧基化产物,随着浓度的增加其缓蚀率增大,但在浓度达到80mg/L后缓蚀率增加很慢。对于季铵化产物,随着浓度的增加其缓蚀率也不断增大,在浓度100mg/L时缓蚀率约可达90%。在相同浓度下,季铵化产物的缓蚀率比乙氧基化产物的高。这可能与环烷酸咪唑啉分子中引进了苄基,加强了缓蚀剂对金属表面的吸附有关。 李文静等将二乙烯三胺和羧酸按摩尔比1:(1.05-1.2)加入带温度计、回流冷凝器、搅拌器、分水器的四口烧瓶,取25-40mL甲苯(或二甲苯)作携水剂。缓慢升温至回流,保持此温度,反应2-2.5 h,随后缓慢升温至220-230℃,反应一定时间。蒸出未反应的二乙烯三胺和携水剂,冷却,即制得咪唑啉产物。由于咪唑啉不溶于水,为了提高咪唑啉在油田污水中的溶解性,进一步增强其缓蚀效果,对其进行水溶性改性实验。将咪唑啉产物加入三口烧瓶中,加热到一定温度,加入三氯化磷、甲醛等改性剂,反应一定时间,冷却,即得水溶性咪唑啉衍生物缓蚀剂。制备的水溶性咪唑啉衍生物缓蚀剂为有机吸附膜型缓蚀剂,为了增强其在高温、高氯离子含量、高矿化度污水中的缓蚀效果,选择磷盐、硫脲等作为缓蚀增效剂,确定了复合缓蚀剂配方:20%-30%主体缓蚀剂、40%-50%磷盐、10%-15%硫脲及20%-30%其他配料。通过实验证实,得到的复配型缓蚀剂的缓蚀率和稳定性高于油田常用缓蚀剂;添加量为10~20mg/L时,即可达到满意的缓蚀效果。对缓蚀剂作用机理研究证实,咪唑啉衍生物为吸附膜型缓蚀剂,缓蚀剂分子由电负性较大的O、N、P等原子为中心的极性基与C、H原子组成的非极性烷基组成。这些性能不同的基团在金属的表面起不同的作用,主要通过物理或化学吸附吸附到金属表面,形成吸附保护膜。缓蚀剂分子中具有未成键电子对的元素可进入金属结构的空轨道形成配位体,从而产生缓蚀剂分子的吸附层,抑制金属的腐蚀。 史足华等将松香、蓖麻油、二乙烯三胺、二甲苯按一定比例加入到不锈钢反应釜中,密闭,通冷却水,升温至120℃,恒温0.5 h,搅拌,升温至160℃,反应2 h,随着反应的进行,生成部分低分子反应产物,用二甲苯作为携带剂将其逐渐蒸出,进入接收器,通过控制冷却水的流量来控制接收器中二甲苯的蒸出速度并计量,再升温至210℃,反应6 h,待二甲苯全部蒸出,即表明已生成咪唑啉化合物,降温至90℃,加入一定量的添加剂和水,使合成的中间体质量分数为62%,最后将得到的产物与水按质量比1:6复配,即得到最终的污水缓蚀剂。该样品的外观为棕红色粘稠液体,pH为8~9,固体相质量分数≥8%,样品易溶于水,无沉淀及分层现象。由于松香型咪唑啉和蓖麻油型咪唑啉化学结构和相对分子质量各异。两者相互补充,能够在金属表面形成致密的保护膜。分子结构中的极性基团吸附在金属表面上,而长尾巴非极性基团由金属表面向溶剂排列。一方面由于缓蚀剂改变了金属表面的电荷状态,增大了腐蚀反应的活化能,使腐蚀难以进行;另一方面非极性基团多数排列在金属表面,形成疏水膜,阻止了与腐蚀反应有关的电荷或物质移动,达到抑制腐蚀的目的。该污水缓蚀剂的优点在于:由松香与二乙烯三胺所合成的松香型咪唑啉在金属表面吸附性好,空间位阻大,形成的吸附膜有缝隙;而蓖麻油与二乙烯三胺所合成的蓖麻油型咪唑啉因相对分子质量小、空间位阻小,能够较好地填补松香型咪唑啉所形成的吸附膜缝隙,两者相互弥补,使得缓蚀剂在金属表面形成比一般咪唑啉型缓蚀剂更加致密的保护膜,抑制了腐蚀的进行。 黄光团等使用长链脂肪酸、多胺、甲醛和三氯化磷等为原料合成了咪唑啉有机膦酸类缓蚀剂。在模拟油田注水条件下,对缓蚀剂性能进行了评价,评价结果表明当投加量达到50mg/L时,缓蚀率可达90%。
本文版权为荆门铸鼎新材料有限公司(www.corosi.com)所有,转载请注明出处。
2013年7月12日
本站关键词: 酸化缓蚀剂 | 酸洗缓蚀剂 | 二氧化碳缓蚀剂 | 润湿抑尘剂 | 缓蚀阻垢剂 | 污水缓蚀剂 | 硫化氢缓蚀剂
|